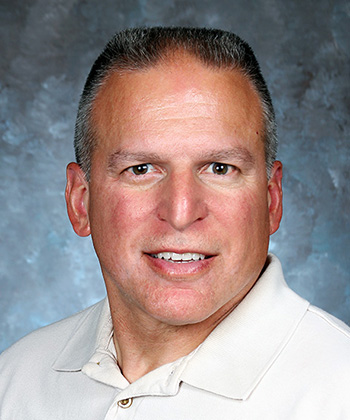
Dan Carrano
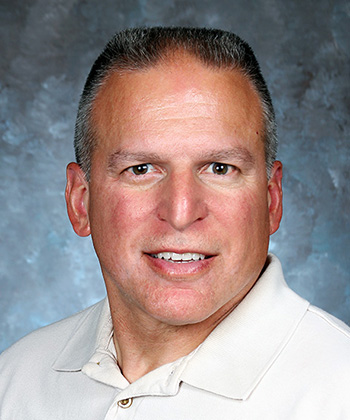
Tell us about your background – what led you to get started in the transportation industry?
My trucking career began shortly after I graduated high school and obtained my first job as a truck driver for a local distributor of restaurant supplies. During this time, I connected with owner-operator truck drivers, and I discovered a passion for helping them maintain and repair equipment. Following this realization, I enrolled in the heavy-duty diesel program at Engine City Technical Institute in Union, New Jersey. Following graduation, I spent ten years working as a truck technician.
As my career progressed, my attention turned to management, but with limited experience, I took an entry-level management position with NJ Transit’s bus maintenance department. I used this time to further my professional knowledge, and in my spare time, I attended technical, leadership and professional development classes. During my six-year tenure with NJ Transit, I worked my way up through the company, eventually becoming a quality assurance manager for vehicle maintenance.
Despite my success, I have always known that my heart was in the trucking industry, so in 2004, I became a manager of vehicle maintenance for New England Motor Freight (NEMF). I remained in this position for almost seven years before beginning with Pyle in 2011 as the Director of Fleet Maintenance. In March of 2019, I was promoted to Vice President of Fleet Maintenance.
What about Pyle attracted you to work for this company?
The equipment, which really should be of no surprise since that’s my area of expertise and interest. As I traveled throughout the northeast during my employment with NEMF, I would always look at the equipment operated by various transportation companies. To this day, I still remember seeing my first Pyle truck in Pawtucket, Rhode Island and I admired the condition and cleanliness of the vehicle, which, in my opinion, speaks volumes about an organization. From that point in time, I started to do some research on Pyle and spoke with many people in the industry, and the feedback I obtained was more than positive.
Describe your role at Pyle.
My position at Pyle is the Vice President of Fleet Maintenance, which entails the purchasing and maintaining of all rolling assets. To help position the Pyle operations team for success, they must have the correct equipment to efficiently and effectively move the customer’s freight. To accomplish this task, I have gained an in-depth understanding of the operational functions to spec and purchase the optimal equipment for Pyle. Then there’s the assignment of maintaining the equipment, which requires a comprehensive maintenance program and a staff of skilled fleet technicians.
What makes Pyle’s fleet maintenance policies different from other carriers?
Most carriers have the same intentions as Pyle’s fleet maintenance department when implementing policies, which are generally focused on standardization and uniformity to improve safety, increase reliability, and reduce cost. However, at Pyle, we also consider what policies will affect the performance of the vehicle and improve the overall satisfaction of our Pyle People.
What are the most impactful changes you have made to the maintenance of Pyle’s vehicles?
In 2014, we implemented a new fleet maintenance software system, which allowed me to tailor the preventive maintenance (PM) intervals. This system factors in the duty-cycle and the requirements of each different make & model of the equipment versus using a broad brush and setting the PM intervals the same across the board on all tandem axle tractors for example. This gives us the ability to dial-in and maximize the PM-inspection schedules while staying within each manufacturer’s specific guidelines.
Tell us about the importance of fleet maintenance.
Vehicles that are properly maintained will operate more efficiently, seeing improved fuel economy, reduced overall maintenance costs, and suffer fewer road-side breakdowns, which ensures the Pyle operations team can provide our customers with reliable service.
Are there any new fleet maintenance initiatives the company is planning to implement this year?
We plan to continue the transition from propane-powered forklifts to battery electric. This initiative has been beneficial for reducing maintenance costs, saving in the operational costs of powering forklifts and an overall improvement in the dock environment due to decreased noise, reduced dust, and the elimination of exhaust emissions.
What achievement are you most proud of during your time with Pyle?
I am most proud of the implementation of safety-related features on the trucks. Most of Pyle’s trucks are equipped with air disc brakes, collision mitigation with active braking, lane departure warning systems, and automated manual transmissions. All of these features working in unison enhances the safety of the vehicle. I continue to evaluate manufacturer options to improve the performance of our vehicles or assist our drivers in performing their job.
Is there any new fleet equipment that is capturing your attention?
Battery electric trucks. Currently, I’ve implemented two Mitsubishi Fuso eCanter class 4 battery-electric trucks operating out of Pyle’s Bronx, New York terminal. These trucks are on a two-year lease, which allows us to experience the different challenges involved with operating and charging a battery electric vehicle (BEV). I am currently researching what new BEV products are available or soon to be released by the different manufacturers, and I believe diesel-powered trucks will continue to be the leading choice of transportation companies for years to come. However, battery-electric trucks will most likely have their place in densely populated urban areas that may be governed by exhaust emission regulations in the future.
What is the most valuable lesson you have learned as a leader?
I learned the importance of mentorship and continual training. Fleet maintenance is a complicated business and requires a total team effort to be successful. It takes years to understand the different aspects (equipment, technicians, parts, vendors, manufacturers) and the importance of relationships. Every chance I get, I try to use situations as training or coaching sessions to advance the team members’ skills in fleet maintenance.
Any closing thoughts?
The transportation industry is a people business and it is important to develop and maintain strong relationships. It takes a small army of talented and reliable people to successfully execute what is needed for Pyle to remain the premier carrier in the Northeast.